
High-Temperature Stainless Steel Ball Valve & Butterfly Valve for Industrial Excellence
In industries where operational conditions push the boundaries of material performance, selecting the right valve is not just a matter of efficiency—it's a matter of safety and longevity. High-temperature stainless steel ball valves and butterfly valves have emerged as indispensable components in managing extreme thermal environments across sectors such as oil and gas, chemical processing, and power generation.
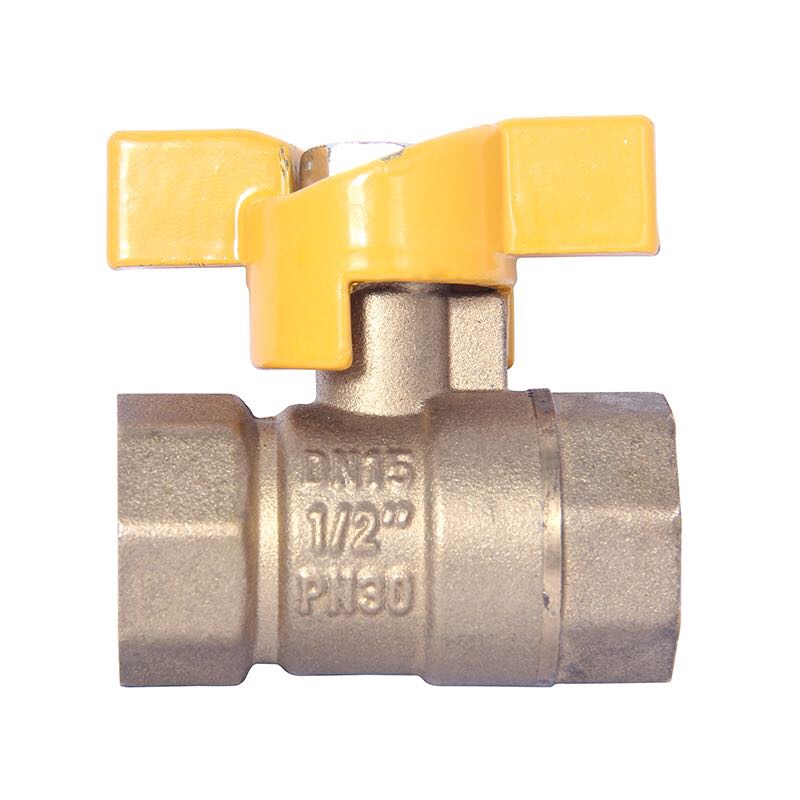
In Limit Environments How to Choose a Reliable Valve?
Operating at elevated temperatures introduces challenges like thermal expansion, oxidation, and material fatigue. These factors can compromise the integrity of standard valve systems, leading to costly downtime or hazardous failures. This is where high-performance stainless steel valves step in—offering superior resilience against heat, corrosion, and mechanical stress. Whether it’s maintaining tight shut-off capabilities or ensuring smooth flow control, these valves provide consistent performance even under the most demanding conditions.
The Secret Behind High-Temperature Ball Valves: More Than Just Heat Resistance
Ball valves are known for their robust design and reliable sealing properties. In high-temperature applications, their construction must be optimized to handle both pressure and heat without sacrificing function. The internal structure typically includes precision-engineered seats and seals that retain elasticity at elevated temperatures, preventing leakage while allowing for easy operation. The use of stainless steel further enhances durability by resisting corrosion from aggressive media such as steam, acids, and solvents.
These valves are especially favored in petrochemical plants, refineries, and thermal power stations, where system integrity is non-negotiable. Their quarter-turn mechanism ensures rapid isolation of flow, minimizing risk during emergency shutdowns or maintenance procedures.

The Power of Butterfly Valves: Lightweight Yet Exceptionally Capable
Butterfly valves may appear simple, but their impact on process efficiency is profound. Designed with a disc that rotates within the flow path, they allow for swift opening and closing, making them ideal for applications requiring frequent adjustments. High-temperature butterfly valves are often equipped with resilient seat materials and reinforced body structures to maintain seal integrity even when exposed to fluctuating thermal loads.
One of the major advantages of butterfly valves lies in their compatibility with automation systems. When integrated with actuators and control units, they enable real-time flow modulation, enhancing process accuracy and reducing manual intervention. This makes them particularly valuable in large-scale manufacturing lines and HVAC systems where energy efficiency and dynamic control are priorities.
Material Matters: Why Stainless Steel Stands Out
While various metals can withstand heat, few offer the comprehensive benefits of stainless steel. Its inherent resistance to oxidation, coupled with excellent mechanical strength at elevated temperatures, sets it apart from alternatives like carbon steel or cast iron. Grades such as 304, 316, and 321 stainless steel are commonly used in valve manufacturing due to their balanced properties of corrosion resistance, thermal stability, and weldability.
Distinguishing a high-quality stainless steel valve involves assessing its metallurgical composition, surface finish, and adherence to international standards like API, ASME, and ISO. A reputable manufacturer will ensure full traceability and provide certifications to back up claims of durability and performance.
The Engineering Behind Precision: From Raw Material to Finished Product
Producing high-temperature valves is a meticulous process that begins with material selection and extends through casting, machining, assembly, and rigorous testing. Each stage plays a crucial role in determining the final product’s reliability. Advanced CNC machining ensures dimensional accuracy, while automated welding techniques guarantee leak-proof joints. Every valve undergoes hydrostatic and functional tests before leaving the factory, confirming its readiness for field deployment.
Customization options such as extended stem lengths, special coatings, and alternative end connections (e.g., flanged, threaded, or welded) make it possible to tailor valves for unique applications—from geothermal energy plants to aerospace testing facilities.
Real-World Applications: Proven Performance Across Industries
Across global industrial projects, high-temperature stainless steel ball and butterfly valves have consistently delivered measurable results. For example, in a Middle Eastern refinery, the installation of stainless steel ball valves led to a 40% reduction in unplanned maintenance over a two-year period. Another case in a European chemical plant saw a 25% drop in valve-related downtime after upgrading to high-performance butterfly valves designed for continuous operation above 400°C.
Engineers frequently praise these valves for their long service life and minimal upkeep requirements. As one facility manager noted, “Switching to stainless steel high-temp valves was a game-changer. We’ve seen fewer leaks, less wear, and overall greater peace of mind.”
Maintenance Tips: Ensuring Longevity Through Smart Care
Even the most advanced valves require proper care to perform optimally throughout their lifecycle. Regular visual inspections, lubrication of moving parts, and checking for signs of wear or leakage are essential routines. It’s also advisable to track operating parameters like temperature fluctuations and pressure variations, which can signal early signs of component fatigue.
Replacing seals or packing at recommended intervals prevents unexpected failures. Always refer to the manufacturer’s guidelines for servicing schedules and spare part specifications to ensure continued compliance with safety and performance standards.
Looking Ahead: The Future of High-Temperature Valve Technology
As industries evolve toward smarter, more sustainable operations, so too do the technologies that support them. The integration of IoT-enabled sensors into valve systems allows for real-time monitoring of performance metrics, enabling predictive maintenance and reducing unplanned outages. Additionally, ongoing research into advanced alloys and composite materials promises even higher temperature thresholds and improved corrosion resistance.
Sustainability is also shaping future developments. Manufacturers are increasingly focusing on reducing emissions during production, optimizing energy consumption, and designing valves with recyclability in mind. As environmental regulations tighten, these innovations will become vital to staying competitive and compliant.
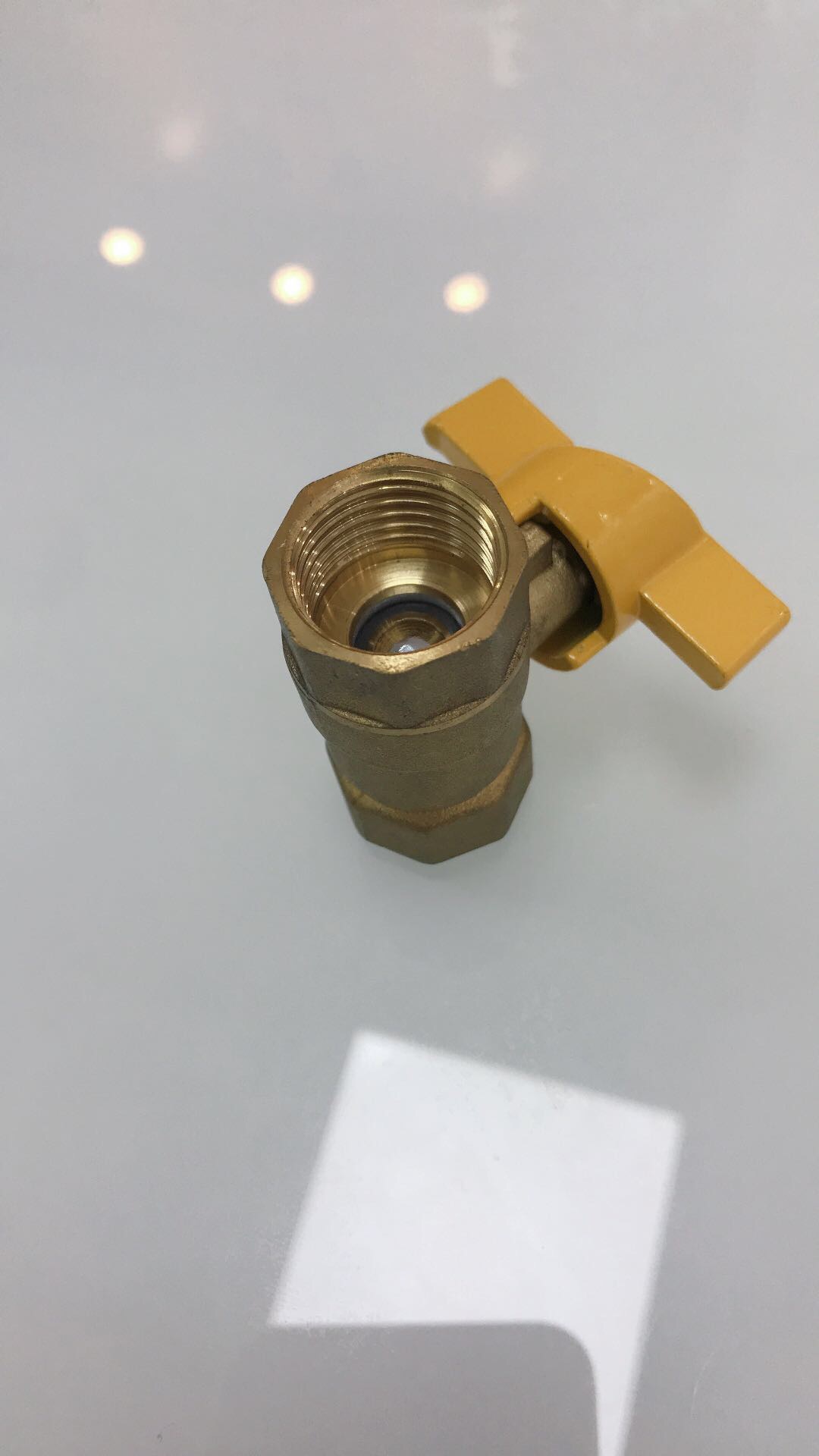
Conclusion: Choosing Excellence in Extreme Conditions
When your operations demand reliability in extreme environments, settling for anything less than top-tier valve technology is simply not an option. High-temperature stainless steel ball valves and butterfly valves represent the pinnacle of engineering excellence—combining durability, performance, and adaptability to meet the toughest industrial challenges head-on.
Whether you're outfitting a new facility or upgrading existing systems, investing in premium-grade valves is a decision that pays dividends in safety, efficiency, and long-term cost savings. Explore our range today and discover how the right valve can elevate your industrial processes to new heights of performance and dependability.
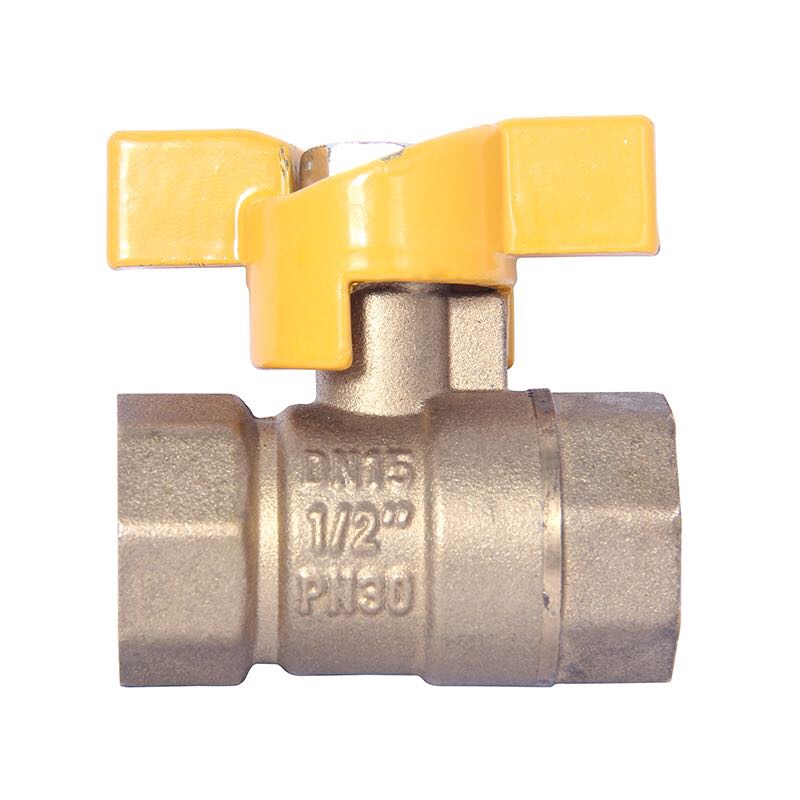