
Grasp the core science of high-temperature fluid control and analyze the special valve system for mold temperature machine
In the complex and harsh industrial production environment, how to accurately control the flow of high-temperature media has become a key issue to determine efficiency and safety. This paper analyzes the core performance differences between the two mainstream temperature control components-mold temperature machine high temperature ball valve and stainless steel high temperature butterfly valve and their respective fields of application.
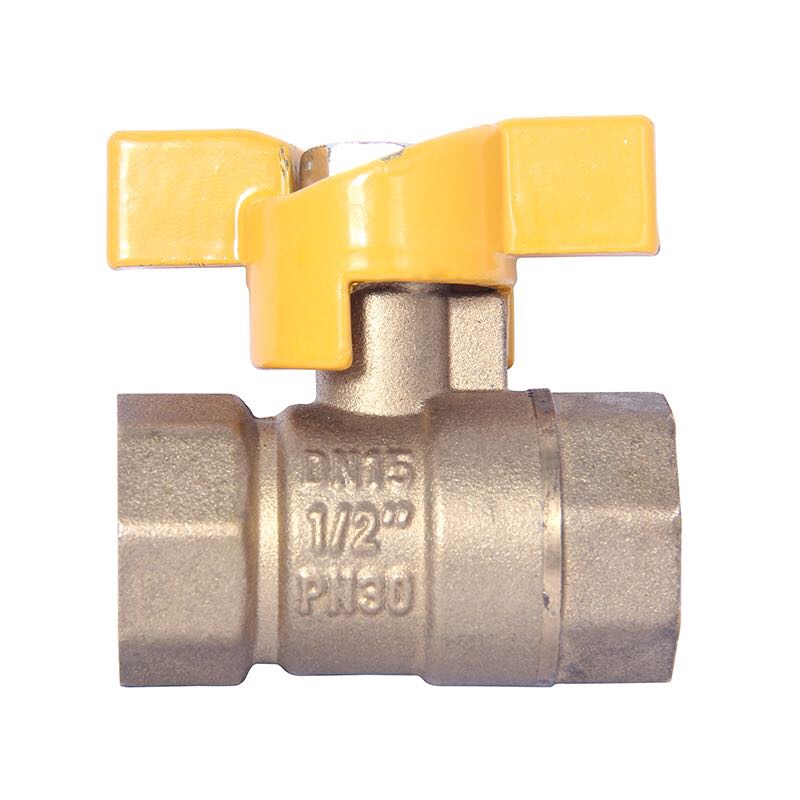
From the material revolution to see the temperature adaptation boundary breakthrough
the face of up to three hundred and fifty degrees Celsius above the challenge of the condition, the traditional valve material is often difficult to do. The new generation of mold temperature machine supporting products has achieved a qualitative leap through innovative material systems: special alloy steel obtains super heat resistance after multiple vacuum heat treatments, and can maintain geometric stability in long-term operation; Nano-scale sealing layer coating technology greatly improves the air tightness and pressure limit of each connection interface; The specially selected duplex stainless steel substrate has excellent tensile resistance and chemical corrosion resistance, it still shows excellent service life in frequent alternating hot and cold environments.
Precision transmission mechanism decoding to achieve flow regulation between millimeters
Through the fine engineering calculation and optimization of actuator linkage components, modern high-end valves have unprecedented control accuracy:
the worm gear drive module adopts a military-grade meshing gap compensation mechanism to ensure that every switching operation can be completed smoothly without vibration and impact. The built-in digital encoder feeds back the current opening value in real time, allowing users to make fine adjustments in 1% scale units. The fully enclosed explosion-proof motor housing has reached IP68 waterproof grade certification, and can operate normally even if exposed to dusty or humid immersion areas.
Panoramic presentation of typical industry application cases
Plastic Molding Production Line | Energy and chemical facilities | Food processing machinery |
---|---|---|
Quickly respond to mold cooling circuit switching commands | Continuous delivery of 350 ℃ heat transfer oil with zero risk of leakage | Accurate metering of edible oil quantitative filling process |
Intelligent interlock protects constant temperature stability of injection molding process | Multiple redundant control systems guarantee continuous operation | Resistance to acid-base cleaners throughout CIP cleaning procedures |
Support remote SCADA monitoring platform data interaction | Flange connection end face meets ASME B16.5 code requirements | Full compliance with EU EC No 1935/2004 food safety contact standard |
End-user maintenance experience sharing
"Since last year, the brand's customized scheme has been completely replaced, the frequency of hydraulic station failure repair in our die casting workshop has decreased by more than 70%."
"It is commendable that after-sales service engineers can recommend the optimal installation angle and torque settings for specific operating conditions."
Future trends
With the wave of intelligent manufacturing sweeping the global manufacturing industry, the new electric control valve is undergoing the following transformative evolution:
cutting-edge models are equipped with micro wireless sensor arrays to continuously collect temperature, pressure and even their own wear information and upload them to the analysis center through the cloud. The edge calculation unit developed based on AI algorithm can predict potential failure nodes according to historical operation and maintenance records and actively remind the spare parts procurement plan. The highly standardized functional module design enables on-site maintenance personnel to complete the replacement of major wearing parts within 10 minutes, completely bid farewell to the past several hours of professional return to the factory repair era.

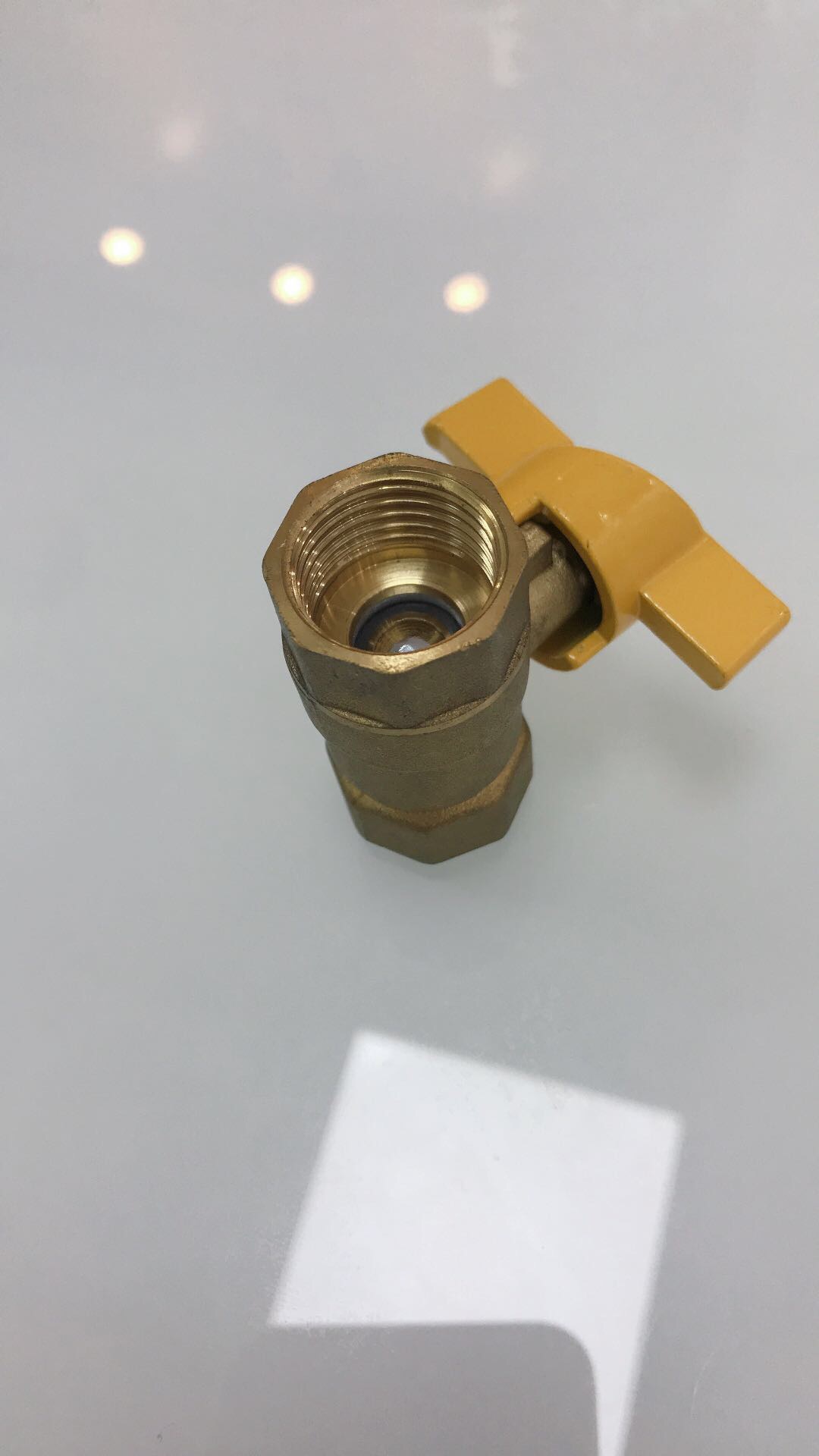